A Solution to Control Valve Deadband Issues: Shape Memory Alloy Actuators
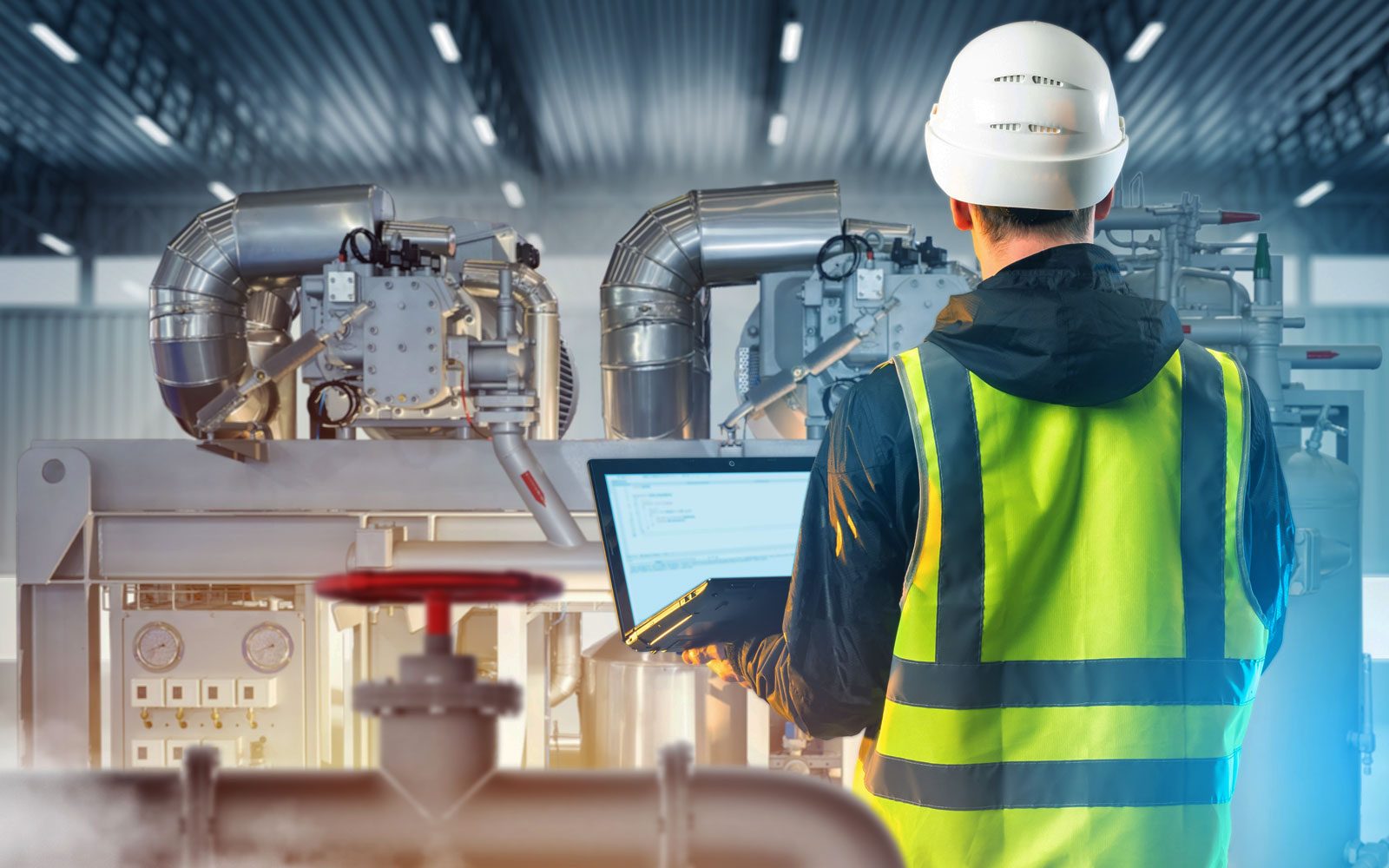
In industrial settings, control valves serve as critical components, regulating and modulating fluid flows to ensure processes operate within desired parameters. Despite their widespread use, control valves, particularly those operated by traditional electric motorized or pneumatic actuators, face a common challenge: deadband (Figure 1). This phenomenon, the control signal’s range that fails to elicit an output, can significantly undermine system performance.
Deadband commonly appears in systems that employ electric or pneumatic actuators, due to either the natural mechanical play or as a deliberate design decision. Designers may intentionally introduce deadband to their system processes to reduce motor duty-cycle for maintaining safe motor temperatures or to reduce the consumption of instrument air in pneumatic controllers. Its impact on the process under control is multifaceted, leading to delayed responses, inefficiencies, oscillations, and the potential for increased wear on components leading to more frequent maintenance. In industries like natural gas, where the precise handling of highly valuable and volatile substances are routine, minimizing deadband is not just a matter of efficiency but of safety and economic viability.

The introduction and adoption of Shape Memory Alloy (SMA) actuators in the industry offers a solution to the deadband issue. These actuators, benefiting from the unique characteristics of SMA technology, provide high precision and responsiveness. Distinct from their typical electric motorized and pneumatic counterparts, SMA actuators boast the ability to operate at 100% duty cycle without backlash or slop, effectively minimizing the effects of deadband. This capability is currently being leveraged in the natural gas sector to enhance the performance and reliability of control systems.
Control Valve Problems from Deadband
The phenomenon of deadband within valve control systems presents a series of challenges that directly influence the operational efficacy, precision, and reliability of process control. Deadband is defined by a range of control signal inputs that fail to elicit any adjustment in valve position and is an obstacle in maintaining optimal process conditions. Below are the key challenges associated with deadband, each underscoring the critical need for refined control mechanisms in industrial settings.

Figure 2: A Kinitics KVA38 Glove Valve Actuator powered by SMA.
- Reduced Sensitivity to Control Signal Variations: The presence of deadband impairs a control system’s ability to respond to changes in the control signal. This reduction in sensitivity can lead to the inability to maintain process variables within narrow tolerances, essential for processes that require stringent control over parameters such as pressure and flow rates.
- Delayed Response to Process Control: Deadband introduces a delay in the valve’s response to alternations in process conditions. In dynamic environments where quick adjustments are essential, such delays can result in process inefficiencies, waste, heightened safety risks, and operational instability.
- Increased Hysteresis: A direct consequence of deadband is the escalation of hysteresis within valve control systems. Characterized by a variation in actuation points based on the signal’s direction of change, hysteresis introduces control inaccuracies, complicating the task of achieving precise process management.
- Reduced Energy Efficiency: The inefficiencies introduced by deadband can lead to processes being either over-operated or under-operated as attempts are made to counteract the imprecision, thereby inflating operational costs and energy usage.
- Increased Risk of Oscillations: Deadband present in the system increases the likelihood of oscillations and system instability. Without proper adjustment of control strategies to accommodate deadband effects, the system may experience undesired oscillations, undermining process control stability and reliability.
Sources of Deadband
Deadband can compromise the precision and efficiency of valve control systems. Understanding and addressing these sources are crucial for enhancing system accuracy and responsiveness.
- Mechanical Backlash: Typically present in both pneumatic and electric motorized valves, mechanical backlash – looseness within actuator drivetrains – introduces a delay characteristic of deadband. Initial actuator movements fail to directly translate into valve adjustments, creating a zone where control inputs do not produce expected outcomes.
- Friction: A universal challenge, friction occurs within the valve mechanism, notably between the valve stem and packing in addition to friction from the several moving components typical of pneumatic or electric motor actuators. This friction requires additional force to both initiate movement and maintain it, contributing to deadband by delaying actuation until a higher input threshold is reached.
- Positioner Issues: Problems with the valve positioner, crucial for adjusting the actuator’s operation based on the control signal, can significantly magnify deadband. This issue is particularly pertinent for pneumatic actuators, where the precision of the positioner is essential for converting air pressure changes into accurate valve movements.
- Duty Cycle Limitations: Typical electric motors cannot run continuously (for example, less than 100% duty cycle) to maintain safe operating temperatures to prevent motor failure. A deadband may be intentionally introduced to prevent motorized actuators from continuous motion in hunting for the process setpoint.


Shape Memory Alloy Actuators: Advancing Valve Control Precision and Response
SMA actuators (Figure 2) represent an advancement in industrial valve control technology. SMA’s possess the extraordinary ability to return to their original shape when energized, a property that SMA actuators harness to offer smooth control of valve position with fine precision and accuracy.
How SMA Actuators Work
Shape memory alloys (SMA) belong to a distinct category of metal alloys capable of “remembering” a predefined shape.
This two-way shape memory effect enables precise and consistent shape manipulation. The core functionality of SMA bundled wire actuators, a type of SMA actuator, is derived from the contraction of SMA wires upon being energized, biased against a mechanical spring. This dynamic converts electrical energy into mechanical movement, facilitating precise and smooth valve adjustments in response to control signals. The application of electrical current to these wires triggers the shape memory effect, allowing the wires to shorten by overcoming the spring force. This contraction, when linked to a valve stem, facilitates the precise regulation of the valve’s position. This ability for precise control allows for extremely fine responses that minimize deadband that arises in control valve applications (Figure 4).
Minimizing Deadband with Shape Memory Alloy Actuators
SMA actuators introduce a suite of advantages directly addressing the issue of deadband:
- 100% Duty Cycle: SMA actuators excel in continuous throttling operation without the need for pauses or downtime, crucial for processes requiring uninterrupted control. This constant operability ensures that there is no lag between control input and actuator response, effectively eliminating deadband caused by operational pauses.
- Micron-level Precision: From the ability of precise control over the SMA’s length adjustments, these actuators can achieve incredibly fine positional precision. This ability directly combats deadband by ensuring precise valve movements and positioning that track the command signal.
- Mechanically Efficient and Reliable: SMA actuators on the market (Figure 2) feature a single moving part in the drivetrain that moves in-line with the valve stem, thus minimizing friction losses due to internal components (e.g., gears, bearings, etc. – typical of motorized or pneumatic equipment). Also, the absence of high-speed rotational components reduces wear, minimizes maintenance schedules, and prolongs actuator life.
Conclusion
SMA actuators represent a solution in combating challenges due to deadband in control valve systems. SMA technology provides the ability for continuous operation at 100% duty cycle with a mechanically efficient drivetrain. When applied to process control, SMA actuators provide precision and responsiveness that mitigate deadband’s negative impact on system performance. SMA actuators are being used in critical industrial applications including within the natural gas sector (Figure 3). Their use provides a reliable solution for process control in a sector that aims to electrify operations including the adoption of electrically powered control valve actuators.
This article was written by Adam Nguyen, Automation Solutions Specialist – Kinitics Automation Limited
and was originally published in Valve World Americas journal.
Reprinted with permission from Valve World Americas, May 2024.